¿Por qué pasar del monitoreo de condición al mantenimiento predictivo? – Parte 1
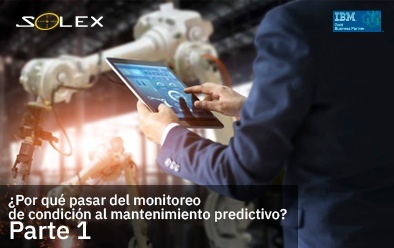
Por Dan Yarmoluk y Craig Truempi | Lectura de 5 minutos.
Solex & IBM Maximo, perfecto para empresas intensivas en activos productivos
En Solex determinamos el licenciamiento adecuado de IBM Maximo, ofreciendo servicios integrales de: implementación, mejora continua, soporte, capacitación, auditoría de la instalación y su uso efectivo.
Solex implementa IBM Maximo, una plataforma de Gestión de Activos EAM de clase mundial que está en capacidad de soportar todo el ciclo de vida del activo, apalancando así la certificación en la norma ISO 55000 y CREG 015 de 2018 y adicional acompañarlo en la Gestión del Cambio.
¿Su organización ha adoptado un mantenimiento predictivo o basado en condiciones?
La adición de estas estrategias de mantenimiento para bombas y equipos industriales heredados o de posventa se promociona hoy como una fuente importante de retorno de la inversión (ROI) para el Internet de las cosas industrial (IIoT). Sin embargo, para muchas personas, el mantenimiento predictivo es un término nuevo. Muchos también confunden el mantenimiento predictivo con el monitoreo de la condición. En esta serie de blogs de 2 partes; desglosaré la diferencia entre los dos, los orígenes de ambos y qué esperar a continuación.
La principal diferencia en el mantenimiento predictivo y el monitoreo de la condición es el momento. Ambos monitorean la salud y la condición de un activo rotativo como una bomba, ventilador, compresor, mezclador, agitador o transportador. Pero el monitoreo de condición se enfoca en condiciones en tiempo real; mientras que el mantenimiento predictivo se ha enfocado en la detección temprana de defectos con 60 o 90 días de anticipación.

Monitoreo de condición 1.0 – 1980 y anteriores
Al igual que las alertas rojas en el tablero de su automóvil, el monitoreo de la condición heredada en un entorno industrial y ha incluido indicadores rezagados como:
- Baja presión de aceite lubricante
- Alta temperatura
- Presión de descarga irregular de la bomba
- Baja o alta presión de sellado
- Nivel bajo o alto del bote de sellado
Una condición de alerta en estas mediciones significa que se ha producido una falla o que ya está ocurriendo y se requiere una respuesta oportuna. En el círculo del mantenimiento predictivo, esto se conoce como «mantenimiento reactivo basado en la condición». El indicador, aunque útil, no da suficiente tiempo para planificar. La producción no tiene tiempo suficiente para planificar y el mantenimiento no tiene tiempo suficiente para alinear las piezas, herramientas y habilidades correctas.
Monitoreo de condición 2.0 – 1990 – 2000
Se adoptó una segunda ola de mediciones que mejoraron drásticamente la detección de defectos. La corriente, la velocidad y la potencia del motor son el resultado de variadores de velocidad que se han implementado para mejorar la eficiencia en el consumo de energía eléctrica. Y las mediciones adicionales de temperatura y vibración son más accesibles. Esto se debe en gran medida a la reducción de costos; la mejora de la confiabilidad, la infraestructura de los sistemas IO y el fácil montaje magnético de los sensores. La segunda ola de mediciones incluye:
- Corriente del motor
- Velocidad
- Poder
- Vibración general
- Temperatura del rodamiento
Una variación en cualquiera de estas mediciones puede indicar una condición de la bomba o sistema de bombeo que necesita atención.
Usando esta segunda ola de alertas para el diagnóstico
El uso de estas mediciones ha resultado fructífero para diagnosticar problemas. Sin embargo, establecer los umbrales de alerta para su uso con alertas automáticas ha resultado ser un desafío. La naturaleza variable del proceso, la receta del producto o la temporada ha hecho comunes las alarmas molestas. Esto ha cuestionado la simplicidad y la claridad del enfoque que requiere para alcanzar el éxito. La corriente, el flujo y la presión del motor pueden variar con las condiciones del proceso y requieren un análisis humano y/o algún tipo de inteligencia para identificar una falla o anomalía en las mediciones que varían normalmente. Por ejemplo, considerando la capacidad de distinguir una corriente de entrada normal de una corriente alta anormal durante las operaciones de estado estacionario. Los usuarios novatos han intentado establecer líneas de base y establecer alertas estadísticas. Desafortunadamente, con los métodos y sistemas tradicionales, esto lleva mucho tiempo y ha resultado en fallas por fallas preexistentes.
ISO 10186 ayudó a mejorar la identificación del problema
La vibración general desplegada con el conocimiento de los estándares de alerta ISO 10186 ha ayudado a identificar condiciones preexistentes. La aclaración de los modos de falla detectados por la vibración general ha ayudado a explicar los errores ocurridos. Los modos de falla detectados por la vibración general incluyen:
- Desequilibrio
- Desalineación
- Flojedad
- Falla de rodamiento en etapa tardía
Mantenimiento Predictivo
La vibración general es una medida directa para detectar y controlar el desequilibrio, la desalineación y la flojedad de un activo rotativo. Las unidades para la vibración total son pulgadas por segundo – pico, que es una medida de velocidad. Hoy en día, la vibración general se calcula a partir de una lectura de aceleración medida con un acelerómetro de $ 100 a $ 200. Esta medición ha existido durante décadas y un estándar ISO, ISO 10816, define cómo medir y establecer umbrales de alerta. Por ejemplo, el estándar ISO 10816 requiere un rango de frecuencia de 2-1000Hz y recomienda niveles de alerta para máquinas típicas en 0.2, 0.5 y 1.0 IPS-Peak para niveles de alerta menores, de advertencia y críticos.
En general, es excelente para detectar la presencia y la gravedad del desequilibrio, la desalineación y la flojedad. Pero muchos dirían que no es predictivo. La vibración general es un indicador de retraso, ya que el problema o defecto ya existe. Sin embargo, encontrar un defecto de desequilibrio o aflojamiento cuando es pequeño tiene un beneficio significativo si las operaciones y el mantenimiento tienen suficiente tiempo para solucionar el problema mientras aún es pequeño. Reparar el problema temprano tendrá como resultado un costo menor que si espera demasiado y soluciona el problema después de que haya causado un daño colateral adicional. Por ejemplo, no querrá esperar hasta que el eje de la bomba se rompa cuando podría haber alineado el motor, la bomba y las tuberías de entrada y salida.

Condición de Monitoreo 3.0 – Mantenimiento predictivo – 2010
Las mediciones de IIoT para el mantenimiento predictivo son muy parecidas a la discusión sobre los indicadores «líderes versus rezagados» de las empresas. El monitoreo descrito anteriormente podría ser bueno pero aún rezagado o basado en la condición.
Para algunos, el mantenimiento predictivo es sinónimo de tecnologías como:
- Termografía infrarroja (IR)
- Ultrasónico
- Prueba de descarga parcial
Rutas mensuales de vibraciones y análisis del espectro de vibraciones por profesionales capacitados y con experiencia.
Con IIoT y su estructura de datos de siete elementos (consulte el artículo sobre Bombas y sistemas de enero de 2019), han surgido sensores más inteligentes, junto con un procesamiento, comunicación, almacenamiento, alertas y traducción más inteligentes.
Nuevos modos de falla dirigidos con mantenimiento predictivo
Los modos de falla a los que se dirige esta nueva inteligencia incluyen la detección anticipada de 60 y 90 días de:
- Defectos de lubricación
- Defectos de rodamientos
- Cavitación
- Falla del sello de la bomba
¿Por qué nos importan estos modos de falla?
Debido a que múltiples estudios de la industria coinciden en que la lubricación es la causa principal de falla en 50-80 por ciento de los activos rotativos. Las tecnologías anteriores de vibración general, o temperatura de los cojinetes, eran simplemente demasiado tarde o demasiado difíciles para establecer alertas significativas. Las fallas en el sello de la bomba se predicen en base al entendimiento de que la causa raíz común de una falla en el sello de la bomba es la deflexión del eje. Un indicador principal de la desviación del eje es la vibración ultrasónica o de alta frecuencia que se transfiere a través de la carcasa del rodamiento a un sensor.
Descargue gratis nuestros ebooks más populares:
- Gestión de Activos con IBM Maximo para el sector eléctrico
- Típicos problemas de Mantenimiento y Operaciones – Soluciones
- Industria 4.0 y Fábrica Cognitiva: Ventajas, desafíos y cómo implementarla
- ¿Cómo obtener el ISO 55000 para la Gestión de Activos y no morir en el intento?
Mire nuestros artículos más populares:
- Diferencias entre gestión de mantenimiento y gestión de activos físicos
- Todo lo que tiene que saber sobre la gestión de activos y mantenimiento EAM
- Gestión de activos ISO 55000: ¿Cómo IBM Maximo y Solex lo ayudan en todo el proceso?
Identificación de defectos con hasta 90 días de anticipación
En la Condición de Monitoreo 3.0, la vibración general en combinación con alta frecuencia o ultrasonidos, brinda la oportunidad de realizar un mantenimiento «predictivo». Aquí es donde se identifica una condición de falla con 60 o 90 días de anticipación, lo que permite que las operaciones y el mantenimiento planifiquen y programen una reparación. Todo hecho con las partes correctas, las herramientas correctas y las habilidades correctas en el momento correcto.
Ahora estamos entrando en la Condición de Monitoreo 4.0
Las capacidades presentadas aquí preparan el escenario para el monitoreo del estado actual de la condición y la introducción de inteligencia artificial en el proceso. En un próximo blog, hablaré sobre esta dramática transformación que ha permitido a las organizaciones innovadoras pasar de la simple identificación de un mal funcionamiento a la corrección proactiva del problema subyacente.
Obtenga más información sobre el mantenimiento predictivo y la gestión del rendimiento de los activos.
Para ver cómo se organiza su organización y los pasos que puede seguir para el mantenimiento predictivo, realice la evaluación APM. Más información www.solex.biz/ibm-maximo
Traducción cortesía Solex. Ver artículo original: https://www.ibm.com/blogs/internet-of-things/iot-condition-monitoring-part-one/
Si desea conocer más sobre IBM Maximo, no dude en comunicarse con nosotros o escríbanos al Whatsapp (+57 3164576123).
En Solex somos una empresa especializada en soluciones World Class confiables e innovadoras, con más de 28 años de experiencia y 200 casos de éxito en organizaciones de América Latina. Somos socios de negocio “Platinum de IBM” y estamos autorizados para implementar IBM Maximo. También, lo ayudamos con las mejores prácticas y estándares para mejorar su eficacia y eficiencia operativa en la gestión de activos alineada a la ISO 55000.